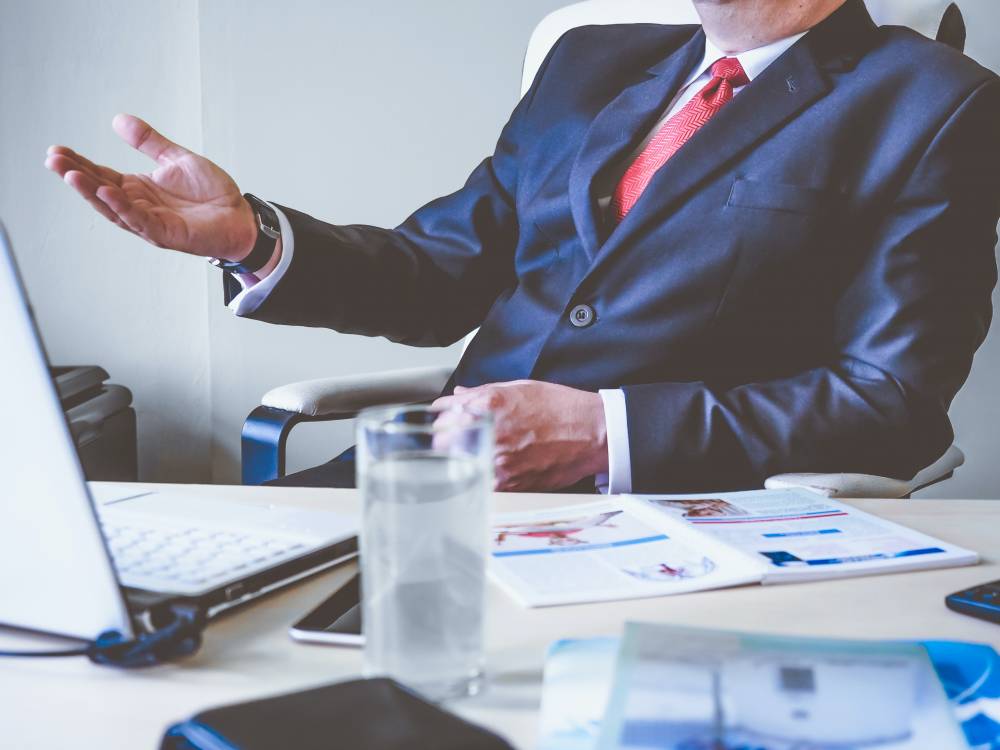
Lean Manufacturing is a production method which originates from Toyota’s 1930 operating model “The Toyota Way” and was developed by Taiichi Ohno. One of Lean Manufacturing’s founders, Ohno dedicated his working life to creating an efficient work process and eliminating toxic activities.
The whole concept of Lean Management is to create a stable workflow in an organization that is constantly improving, becoming more efficient, and of higher quality. This is done by eliminating wasteful activities in the company. In Lean, waste is considered as activities that consume the company’s resources but bring no rewards or value to the customer.
These waste activities can be sorted into 2 different categories. Necessary waste; activities which don’t add value but are necessary, and pure waste; activities which don’t add value and are unnecessary. We can cut out any forms of pure waste immediately; they lower profitability, increase costs, decrease the quality, and lower employee satisfaction.
It’s important to note that not all activities which seem wasteful can be cut; some are essential to the workings of the company. You will have to look at the bigger picture in order to determine which tasks are disposable.
Here are the 7 wastes of Lean in detail, you can improve or eliminate from your company.
When you are moving resources/materials from one place to another without adding value to the product, you are creating waste. Moving your materials around is not only costly, but it also requires attention and is therefore time-consuming. What’s more, excessive moving of your products and materials can damage their quality, taking away from their value. Decrease the amount of transportation and you increase the time and money that can be spent on other, more important things.
The unnecessary movement of employees or machinery is another waste of Lean which can be eliminated from the production process. Especially when the motions required are complicated, production time is increased, and there is a higher risk of accident and injury. When creating your manufacturing process, it is important to make it as easy and straight-forward as necessary. Don’t give your employees unnecessary, time-consuming tasks. Give them only the tasks they need to finish their job.
Having an excess in your inventory “just in case” there’s a huge surge in demand for one of the products doesn’t add value to your company. Overstocking takes up space and is more often than not, unnecessary. Companies overstock in case there is an unexpected demand, and to save them from production delays and “out of stock” labels which might deter customers from buying. However, having more than you need has more disadvantages than advantages.
When you overproduce, you create excess items that the customer is not willing to pay for. This in turn loses your company money in the production process. Overproduction actually causes the other 6 wastes of Lean to appear; more products mean more transportation and movement, a larger inventory, greater waiting time, and the risk of more defected products. Calculating and producing what the customer needs is a sure-fire way to avoid overproduction and clean up the entire manufacturing process.
When the work that you do doesn’t bring additional value to your product, you are wasting your time, effort, and money unnecessarily. Adding extra features to your products which aren’t useful and provide no value to the customer increases business costs with no extra reward. Extra features that no-one is going to use but that raises the price of your product is considered an unnecessary addition. Nobody benefits from these anyway, so it’s best to leave them out.
When you have defected work, the sub-par items will either need to be reworked or become scrap. Both of these are a waste of time, money, and materials. In some instances, companies may create additional areas dedicated to reworking defected goods, spending money not only on the new space but also on tools and on hiring new employees. When you get it right the first time, there’ll be no need for reworking products or discarding them as scrap.
Waiting is one of the easiest and more important types of waste that you can eliminate. When your resources and tasks aren’t moving or aren’t getting done, precious time is being wasted – and as any busy person will know, time is our most precious commodity. This is why it’s so easy to recognize and eliminate waiting time. If you have products waiting for delivery, machines waiting to be fixed or document awaiting approval, speed the process along, and avoid wasting time.
These 7 forms of waste are not only time, money, and energy-consuming, but they also add zero value to anybody involved. In short: they are unnecessary and can be eliminated.
When it comes to Lean Management, the 7 wastes aren’t just found in production and manufacturing companies; they can be found in anything from software development, marketing project management, etc. If you look closely, you’ll see that they can be applied to pretty much all companies, though they differ from business to business.
Where in Manufacturing, Transportation could be interpreted literally, in Marketing you could interpret it as switching from one task to another or having frequent interruptions. In Software Development, Motion could be classed as having unnecessary meetings. In Project Management, Defects can be considered as collecting information incorrectly. They different wastes can take different forms depending on the type of company.
Identifying the forms of waste that are happening in your company will help you improve your working environment, optimize your resources, and increase your profit.